Whitey-
Apprentice elf
- Thread starter
- #46
The ghosts I think were $1.50 from Woolworths.
Again 1.2v and a single LED (at the top of the ghost). I shoved in 2x WS2811b strip LEDs at the bottom and hot glued them down. I ran only an ingress connector to them because a) they're very small and b) they make sense as a final piece per run.
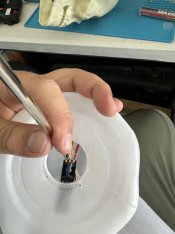
I was pretty concerned they wouldn't look very good, as the plastic diffused heavily during the day. However in the dark they looked great.
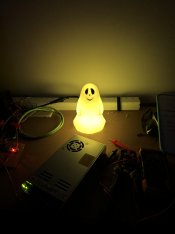
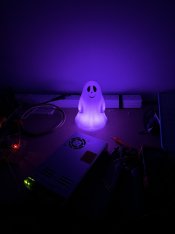
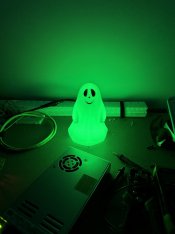
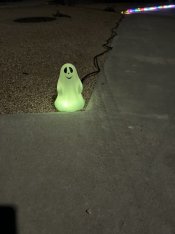
Again 1.2v and a single LED (at the top of the ghost). I shoved in 2x WS2811b strip LEDs at the bottom and hot glued them down. I ran only an ingress connector to them because a) they're very small and b) they make sense as a final piece per run.
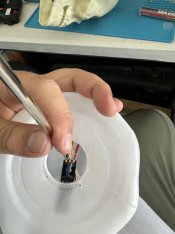
I was pretty concerned they wouldn't look very good, as the plastic diffused heavily during the day. However in the dark they looked great.
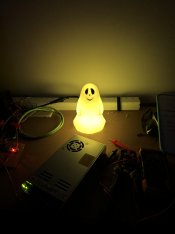
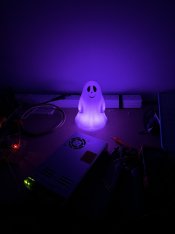
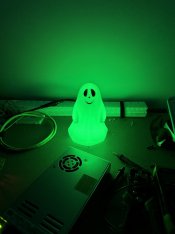
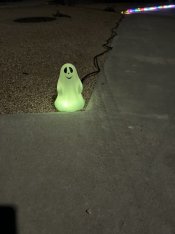